Solid or liquid? Discover with our viscometer the differences between liquids
The Ball Drop Viscometer is based on the Höppler measurement system and is designed to measure the viscosity of Newtonian liquids. To do this, it uses the different rate of fall that a solid sphere presents in the bosom of a liquid depending on the viscosity of it, which, in turn, will depend on its temperature, decreasing with this unlike what happens with the gases.
FL 14.1 – VISCOSITY AND RESISTANTE COEFFICIENT DETERMINATION
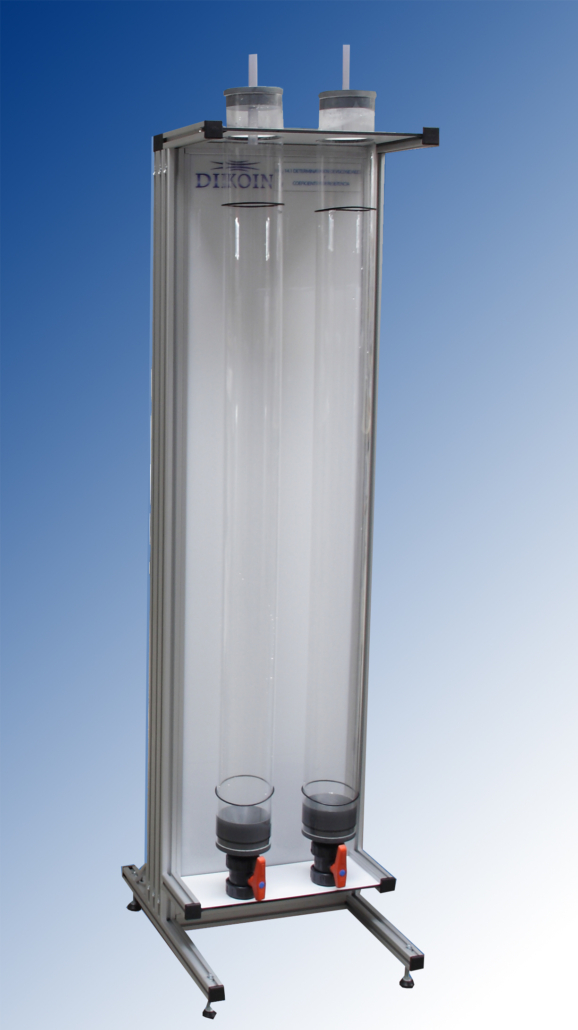
DETERMINATION
Two types of fluids are mainly distinguished:
Newtonian fluid
“A typical fluid.” A fluid is said to be Newtonian if its viscosity — the measure of a fluid’s ability to resist flow — varies only in response to changes in temperature or pressure. Viscosity is the same for all shear rates applied to the fluid. Examples of these types of fluids are: water, sugar solutions, glycerin, silicone oils, light hydrocarbon oils, air and other gases.
FL 14.1 – VISCOSITY AND RESISTANTE COEFFICIENT DETERMINATION
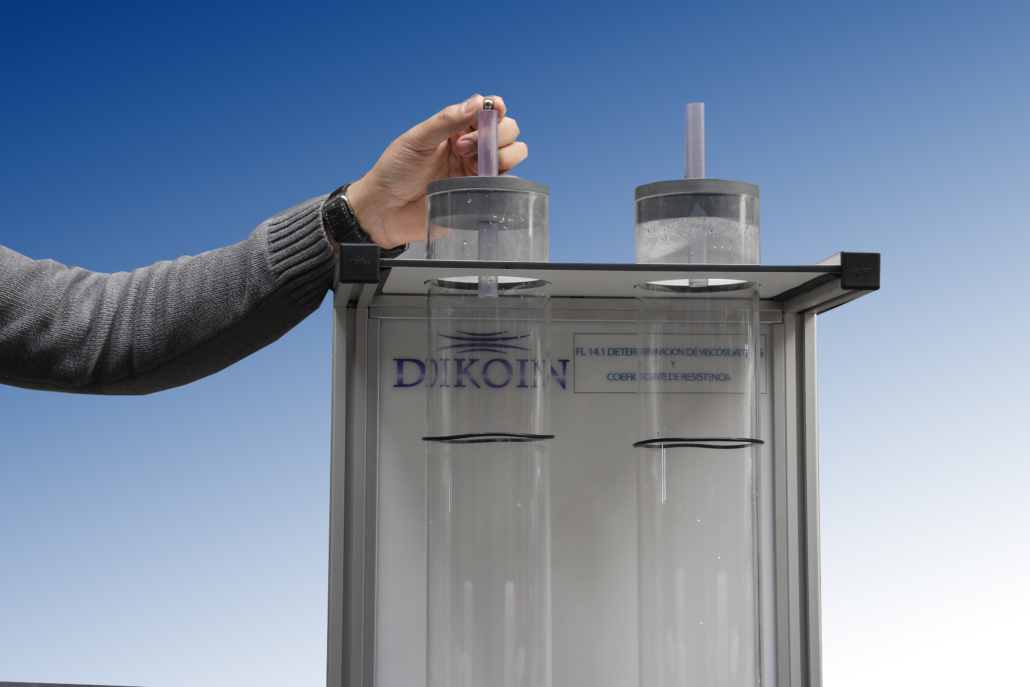
DETERMINATION
The non-Newtonian fluids
“It is not a typical fluid.” Unlike a Newtonian fluid, which behaves exclusively like a liquid, a non-Newtonian fluid has the properties of a liquid and a solid. Under certain conditions, a non-Newtonian fluid flows like a liquid and under other conditions, it exhibits properties of elasticity, plasticity, and strength similar to those of a solid. In addition, unlike Newtonian fluids, the viscosity of many non-Newtonian fluids varies with shear rate.
Non-Newtonian fluids are classified based on how their viscosity varies in response to the duration and magnitude of the applied shear rate.
They are non-Newtonian fluids:
• Thixotropic fluids, in which the viscosity decreases over time when a shear stress is applied. For example, honey in a solid state turns liquid after constant stirring.
• Rheopectic fluids, in which the viscosity increases with time when the shear stress is increased. For example, the cream thickens after constant stirring.
• Pseudoplastic fluids, the viscosity decreases with increasing deformation speed; These fluids exhibit shear-stress fluidization-type behavior. For example, ketchup flows out in a stream at high speed through the hole in the spout of a bottle, but remains stable when served as a portion on a plate.
• Expanding fluids, viscosity increases with increasing deformation speed; these fluids exhibit shear-thickening-type behavior. For example, the fluid made based on the mixture made with corn starch and water as you can see in the experiment in the following video.